〠Instrument R & D 】 In addition to high specific strength, specific stiffness, excellent thermal conductivity and electromagnetic shielding, magnesium's damping performance is significantly better than most engineering metal materials, even comparable to some commonly used polymer materials, but its strength and Heat resistance is significantly higher than polymer materials.
Therefore, it has obvious advantages in shock absorption, energy absorption and noise reduction. The strength, stiffness, plasticity and fracture toughness of magnesium and its alloys are still lower than those of steel and aluminum alloys, and their high temperature creep resistance is poor, which restricts their wide application. As we all know, the strength and damping performance of metal materials are in a contradictory inverted relationship. On the one hand, the strength can be improved by limiting the movement of dislocations. On the other hand, damping requires dislocations to move easily and get rid of pinning, which leads to dependence. The classic material strengthening method must be at the expense of damping performance. How to achieve the toughness and toughness of magnesium and magnesium alloys without significantly increasing the density and reducing the damping performance has become a challenging key scientific issue.
Compared with man-made materials, the macro-mechanical properties of natural biological materials are usually significantly better than the simple sum of their basic structural units. The origin lies in their complex, multi-scale self-assembly structure. Such as shells, bones, etc. present a three-dimensional interpenetrating structure at the microscopic level, and the constituent phases are kept connected and interpenetrating with each other, thereby achieving the complementary advantages of the constituent phases in performance and function, and the simultaneous strengthening and toughening of the materials. The understanding of the magical "structure-performance relationship" in nature provides unique ideas for designing new materials with excellent comprehensive properties.
Recently, in response to the performance requirements for material shock absorption and energy absorption in the fields of aerospace and precision instruments, Liu Zengqian, Zhang Zhefeng, Materials Fatigue and Fracture Laboratory, Institute of Metal Research, Chinese Academy of Sciences, Li Shujun, Yang Rui, Titanium Alloy Research Department, and the University of California, USA Berkeley and the Chinese Academy of Engineering Physics have collaborated to learn from the concept of three-dimensional interpenetrating microstructure of natural biomaterials and melt-impregnated magnesium into the nickel-titanium alloy framework manufactured by additive to build a lightweight, high-strength, high-damping, high-absorption Can magnesium-nickel titanium bionic composite material.
The microscopic three-dimensional interpenetrating bionic structure not only realizes the complementary and combination of the performance advantages of the nickel-titanium reinforced phase and the magnesium matrix, but also gives the material shape memory and self-healing functions. First, interpenetrating the constituent phases in three-dimensional space is conducive to promoting the stress transmission between each other, weakening the stress concentration, making the deformation of the two phases more coordinated, and better exerting the strengthening effect of the nickel-titanium reinforced phase, the strength of the bionic composite material is significantly higher For simple superposition based on the mixing law.
Secondly, the matrix and the reinforcing phase in the biomimetic composite not only depend on the metallurgical combination of the interface, but also have a three-dimensional interpenetrating mechanical interlock, which effectively avoids premature failure caused by interface cracking and gives the material good damage tolerance. Thirdly, the penetration of the constituent phases in the three-dimensional space of the bionic composite material not only fully retains the damping performance of the magnesium matrix, but also the weak interface combination between the two phases can introduce new damping mechanisms such as micro-yield and micro-cracks to further improve the damping performance . In addition, in a specific temperature range (> 150 ℃), the shape memory effect of the nickel-titanium reinforced phase framework has a coupling effect with the creep behavior of the magnesium matrix. The recovery stress of the nickel-titanium is much higher than the creep stress of the matrix, making the deformation damage The bionic composite material can be restored to its original shape and strength by conventional heat treatment to achieve the dual effect of shape memory and self-repair function, and can be recycled repeatedly.
Through multiple mechanisms to improve strength and damping performance respectively, the new bionic composite material breaks through the mutual restraint relationship between the two, and achieves a good combination of strength, damping and energy absorption efficiency of magnesium alloy, and its comprehensive performance is better than the current Known engineering materials are expected to become new types of damping materials for precision instruments, aerospace and other fields.
The above work was recently published in Science Advances 6 (2020) eaba5581. The first author of the article is Zhang Mingyang, a PhD student at the Institute of Metals. Related work was supported by the National Natural Science Foundation of China, the "Xingliao Talents Program" and the Chinese Academy of Sciences Key Frontier Science Research Program.
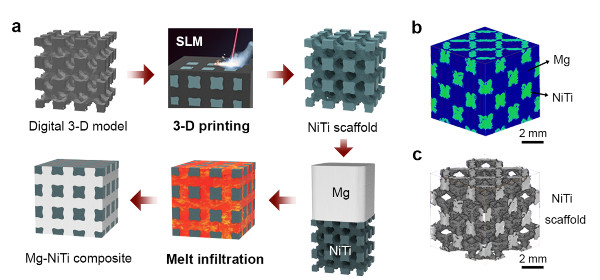
Ironworker,Metal Ironworker,Ironworker Machine,Universal Ironworker
WEISS MACHINERY CO., LTD. , https://www.weissmachinery.com