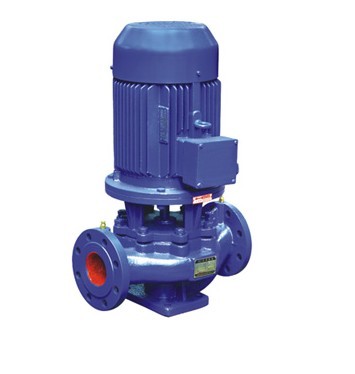
However, there are still many gaps in the domestic pump compared with foreign countries. First, the standardization, serialization, and generalization of the pumps are poor. Each pump manufacturer has its own series, parts are standardized and interchangeably low, and there is a lack of uniform standards. The product specifications and models cannot meet the needs of petrochemical development. The second is poor quality and reliability, mainly due to the lack of domestic varieties of corrosion-resistant materials or improper material selection and processing accuracy. In addition, the seal life of the pump is low and the variety is small.
The life of mechanical seals in foreign countries can generally reach two years or so, and domestic petrochemical pumps have not yet reached this level. The third is the low efficiency of the pump. Due to the poor hydraulic design of domestic pumps, the processing accuracy is not high, and the pump efficiency is generally 2%~3% lower than that of foreign countries. Therefore, many chemical process pumps have to be imported from abroad. In recent years, many domestic pump manufacturers have introduced advanced technology from abroad, which has greatly improved the technological level of petrochemical pumps.
In the future, with the continuous development of petrochemical industry technology and scale, the demand for petrochemical pumps will increase. In addition to continuing to increase the quality of conventional pumps and expand the variety of specifications, the demand for pumps for the transport of corrosive materials is increasing, such as ethylene crackers, polyethylene units and polypropylene units in ethylene production; in chemical fiber production PTA device (pure terephthalic acid), polyester device and polyester spinning device. Therefore, efforts should be made to develop corrosion-resistant pump technology. At present, the materials of corrosion-resistant pumps are still largely made of ferrous materials and high-nickel alloy materials. In the future, they are required to use more excellent corrosion-resistant materials such as titanium, zirconium, and hafnium, as well as non-metallic materials such as ceramics, fiberglass, and graphite. .
Pipes are of qualified mechanical behaviour,
meeting China national & international standards requirements.
drill pipe
Linzhou Fengbao Pipe Industry Co.,Ltd. , https://www.cfbpcoltd.com