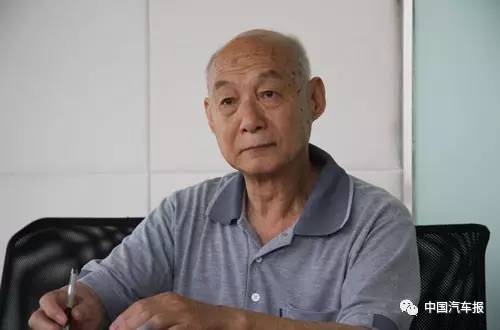
"The quality of auto parts is produced, not checked." Recently, this viewpoint, which Chen Guangzu, the original secretary-general of the China Automobile Industry Advisory Committee raised at an industry conference, has aroused great repercussions.
For a long time, many domestic auto parts companies have superseded the role of inspection in improving product quality, and even thought that the quality of products is checked out. Such quality inspections are off-line (out-of-line) inspections, that is, sampling every few hours, manual analysis, and then guided production based on the analytical values. The time of offline detection lags far behind and cannot meet the quality control requirements of the production line. Chen Guangzu pointed out that under modern production conditions, this is an outdated concept and practice of quality assurance.
Mass production is a feature of modern auto parts production. The quality of human inspection, the use of a large number of offline testing equipment, can not meet the pace of mass production, consume a lot of human resources, increase production costs.
Auto parts are products with technical content, and the assembly of many parts “cooperate†is the whole vehicle. The appearance of faults in auto parts is often caused by the interaction of various factors. The fault correlation and failure transfer between parts are also very complicated. Off-line inspection technology has so far been difficult to accurately locate many automotive faults. Therefore, the determination of the responsible party is also more difficult. For example, an engine failure may not be due to quality problems in the product itself, but rather to oil or other cooperating components.
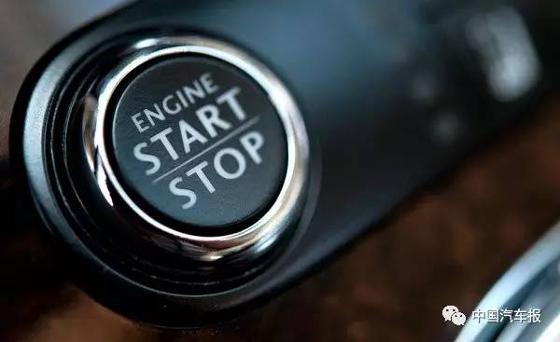
Chen Guangzu also cited the case of an auto start-stop system. After this technology was widely respected and confirmed by the European Union as the standard for cars, it was discovered that this technology, which is both fuel-efficient and environmentally-friendly, will greatly increase the failure rate of bearing bushes. If people do not understand this, it is unfair to blame the fault on the quality of the bearing. It can be seen that the identification of many fault sources requires technical support and time trials. It is difficult to draw correct conclusions just because of a momentary inspection.
Chen Guangzu said: “The quality of auto parts should be ensured by a scientific and effective manufacturing system. Auto parts companies should concentrate on strengthening the quality management and supervision of the production process and ensure the quality of products. They should not rely on off-line inspections where large amounts of funds are required. ."
Modern auto parts companies incorporate raw materials, product functions, quality, and prices into their designs, and should pay attention to quality assurance issues when designing products. The high quality of auto parts also comes from advanced management systems.
Chen Guangzu particularly promoted the Six Sigma management method. Sigma was originally a Greek letter δ and was used to statistically represent the standard deviation value to describe the degree of deviation from the mean of the individual. The measured σ represents a unit defect or defect/million.
6 Sigma is a management strategy proposed by Motorola engineer Bill Smith in 1986 and improved by the United States General Electric Company (GE) in 1996 to form a brand-new high-quality assurance method for manufacturing. This strategy mainly emphasizes the establishment of extremely high indicators, data collection and analysis results, and reduction of product defects. 6 Sigma focuses on process improvement, pursues zero defects, guards against product quality risks, reduces costs, and increases production efficiency, market share, customer satisfaction and loyalty. Six sigmas are 3.4 turnovers/millions of opportunities. That is, 99.99966% of all processes and results are non-defective, indicating that the quality defects of parts and components are close to zero. This is called “zero defect†management level, which means management excellence and competitiveness. Strong and customer loyal.
Chen Guangzu introduced: “The internationally advanced auto parts companies have reached 6 Sigma. The average quality level of China auto parts industry is 3 Sigma to 4 Sigma.†3 Sigma is 66800 turnover/million chance, which means Corporate management is often uneven and uncompetitive. Four sigma is 6210 turnovers/millions of opportunities, which means strong management and operational capabilities and customer satisfaction.
Three Sigma to four Sigma operators are required to make up for or correct afterwards with sales of 15% to 30%. Companies that have reached six Sigma make up for the fact that the funds used have been reduced to 5% of sales.
Chen Guangzu also advocated that auto parts companies replace offline inspections with on-line inspections. On-line inspection is through equipment directly installed on the production line, real-time detection and real-time feedback using soft measurement technology, so as to better guide production and reduce waste. On-line continuous inspection technology has become one of the key technologies in modern process industry and process control. Its successful application can make the quality assurance of auto parts production process more ideal.
Particularly Recommended Yellow Rice Wine
Shaoshing Wine,Hua Diao Yellow Wine,Yellow Wine 20Years,Particularly Recommended Yellow Rice Wine
ZHEJIANGGUYUELONGSHAN SHAOXING WINE CO.,LTD. , https://www.chinashaoxingwine.com