Two types of investment cast processes: Silica Sol process and the water glass process.Â
The Silica Sol process is used to cast complex high quality parts with requirements of a very good surface finish and close dimensional tolerances.Â
This process can range from a weight of just a few ounces to approximately 80 pounds. If you are concerned with precision in very small parts, we are especially proficient at very fine detail work including teeth and serrations.
The water glass process is typical of the process in the early stages of investment castings. It generally is capable of much larger castings than the Silica Sol process, but does not have as good of surface finish or tolerances. The water glass process provides parts that have better surface finish and dimensional tolerances than sand castings.
This process may range in weight from several ounces to approximately 200 pounds.
First article layouts and spectrometer material certifications are provided with all first article samples.
Custom service:Â A variety of secondary operations can be performed on both types of investment castings. They include heat treatment, machining, plating, painting, polishing and buffing, assembly services and even custom packaging.
Production process:
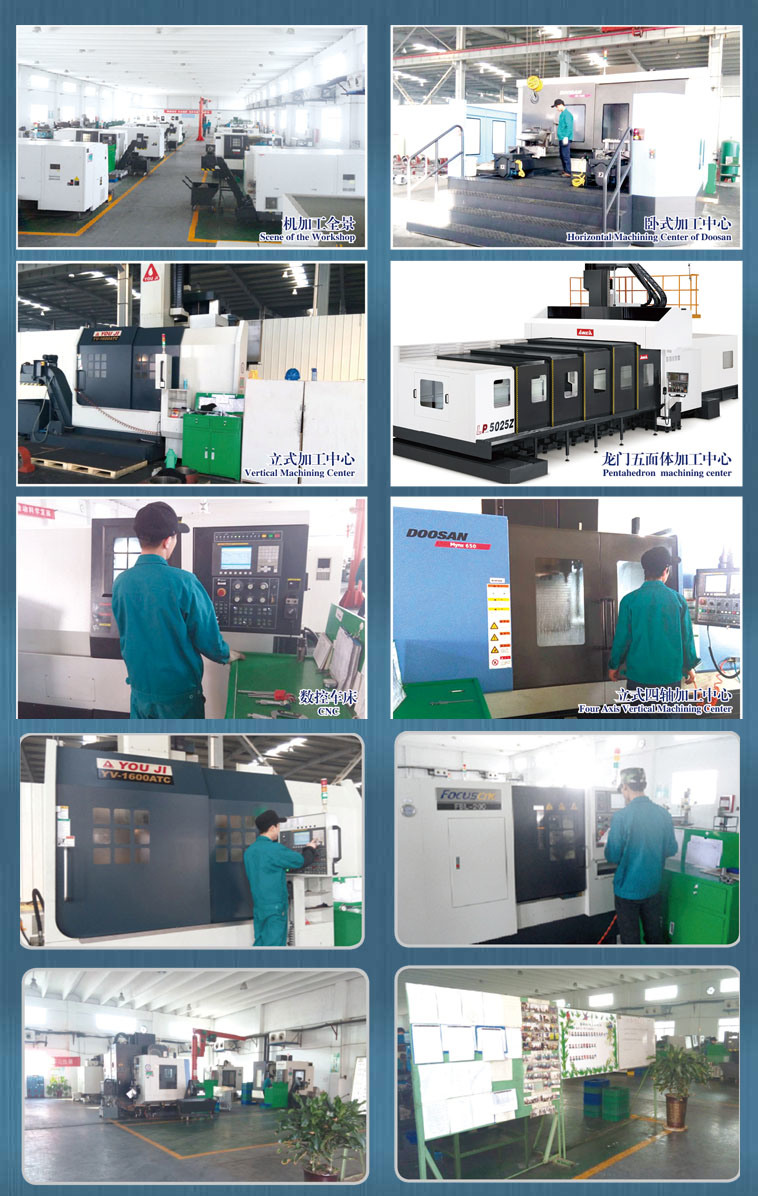
Materials that are available:
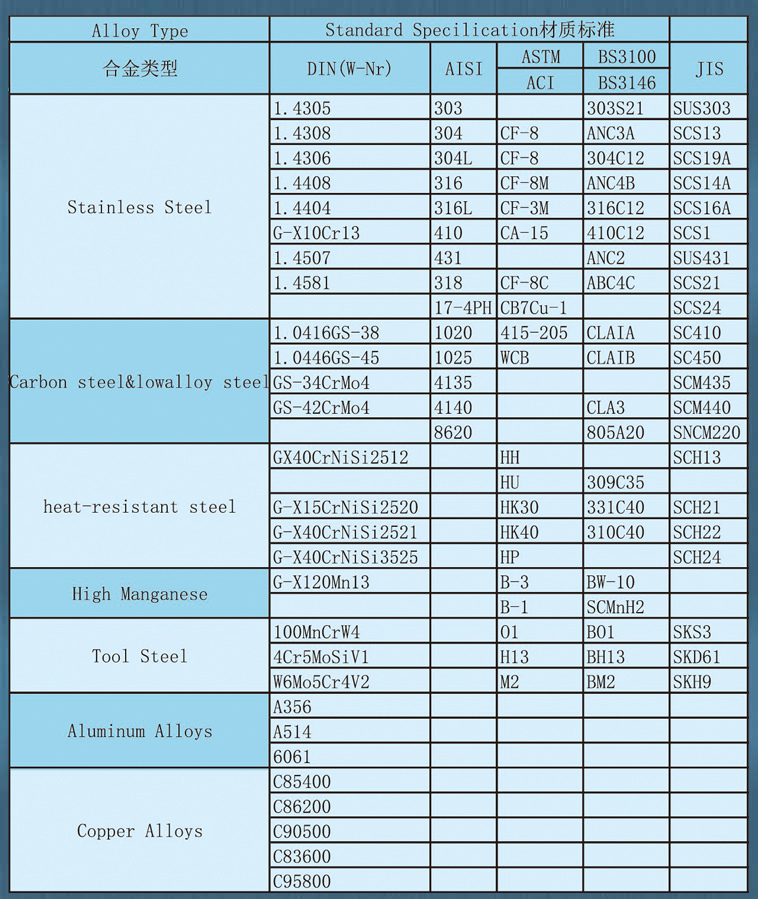
Products show:
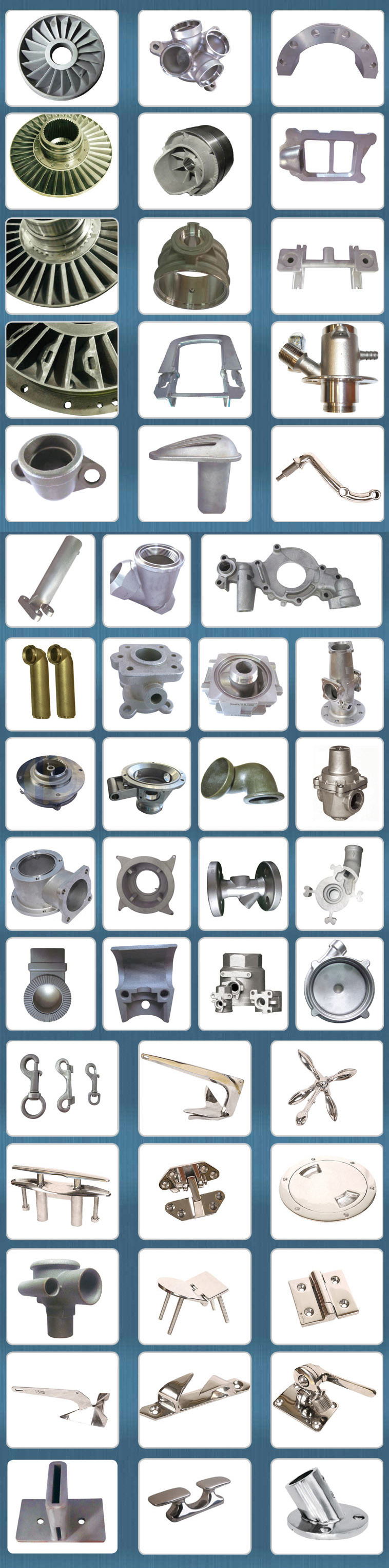
Packaging & shipping:
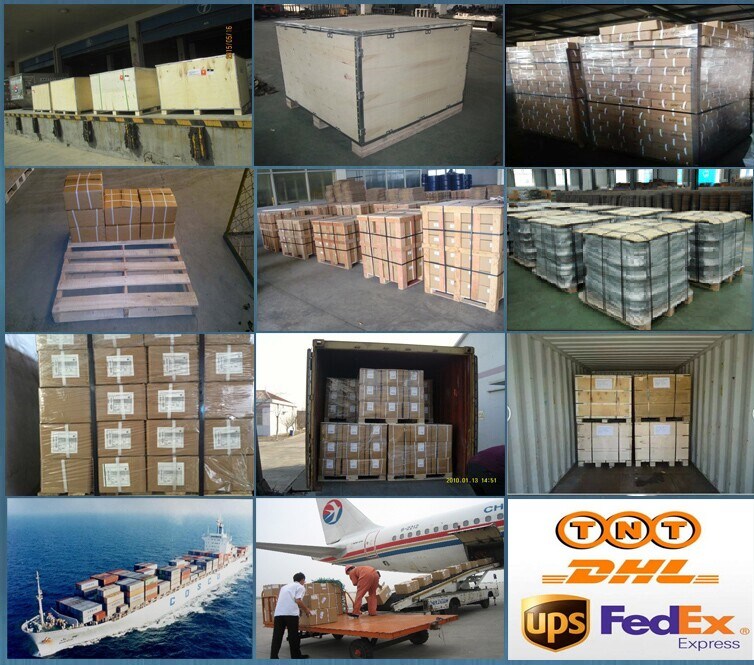
Our customers:
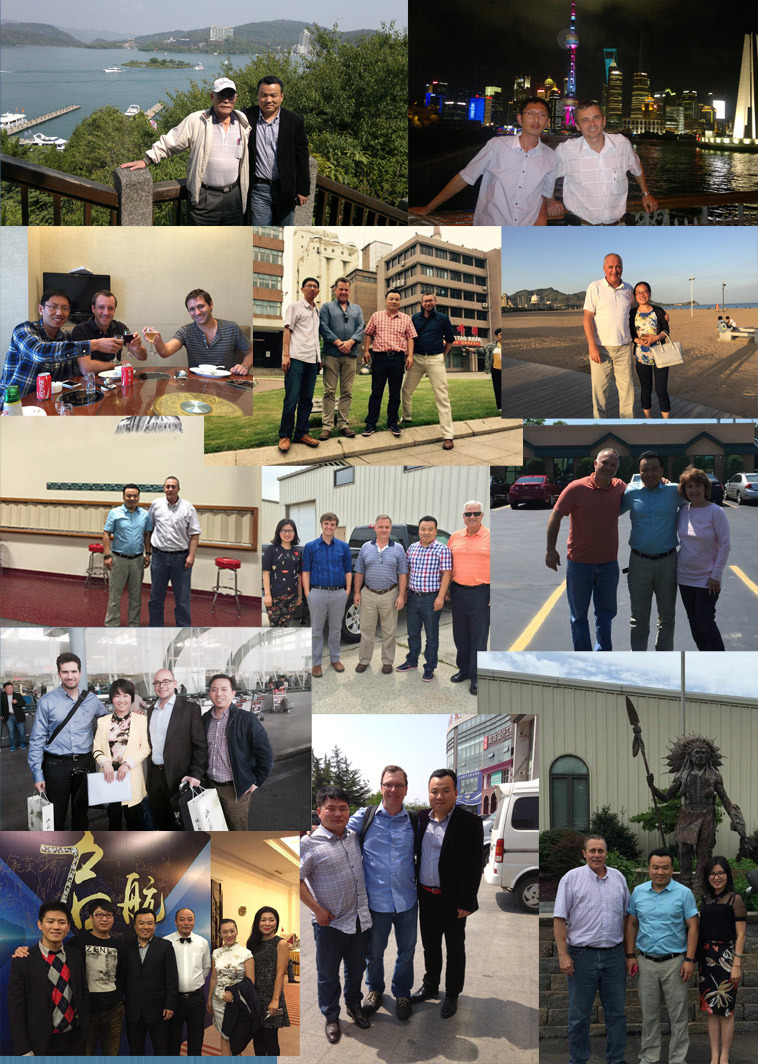
Our service:
Â
1. 20 years of manufacturing success in China and exporting experience worldwide |
2.Global specialized producer of machined castings. |
3. We combine our own resources with some other well-developed factories to fulfill a wide range of contract manufacturing capabilities. Working with one source, saves time and money. |
4. Satisfied supplier of 7 big companies from North America and Europe. |
5. Low cost mold materials and focus on efficiency offer a cost effective solution to your metal component purchasing requirements. |
6. Normal lead times range from 1 to 6 weeks for fully-machined components. |
7. Strong capacity to help customers develop new projects. |
8. Our sales department is 24 hours available in order to help our customers solve problems quickly. |
FAQ:
1. Can we get the samples?
Yes, we can supply you the samples for checking our quality within 10-30 days.
2. Can we place a trial order first time?
Yes, we are glad to supply you small trial order, and hope your quantity will be big in future.
3. Can you help us to do the customs clearance of import?
Yes, we can help you to do the customs clearance.
4. What is your lead-time?
With our design, fabrication and manufacturing skills and experience, we can efficiently exceed your expectations and meet the time frame required. However, we guarantee that quality and service are never compromised.
Â
Intergrated Design Batch Waste Tyre Pyrolysis Plant
Pyrolysis Plant is used for recycling waste tire, waste plastic, waste rubber to fuel oil. According to the actual situation in every country and district, we developed different models of Batch Pyrolysis Plants for waste tires, rubber and plastic with daily capacity 5 -10 tons.
Flowchat of Batch Waste Tyre Pyrolysis Plant
Advantages of Batch Waste Tyre Pyrolysis Plant
1. Full open door design: Speedy loading in and steel pulling out; Easily cooling down after one batch finished, saving time; No leaking with special high temperature flexible graphite packing.
2. Unique Craft Condensers: High condensing efficiency with more oil output. Good quality oil, longer lifetime, and easy to clean.
3. National Patent Unique Smoke Scrubbers: More efficient removal of the acid gas and dust of the smoke by neutralization, purification and absorption, environmental friendly without pollution.
4. National Patent Carbon Black Discharging System: Speedy fully enclosed Auto-discharging under high temperature, avoiding carbon black pollution, saving time.
5. Automatic Submerged welding technology, ultrasonic nondestructive testing, both manual and the automatic safety devices.
6. Sync Gas Recycling System: Fully burned after recycling and utilization, saving fuel and preventing pollution.
7. Direct Heating System: Enlarging heating square to lengthen the lifespan of the reactor and easy to control the temperature.
8. National Patent, unique heat insulation shell; high efficiency temperature keeping, excellent energy-saving effect.
Technical Parameter of Batch Waste Tyre Pyrolysis Plant
NO. |
ITEM |
PROJECT |
|
1 |
Equipment Model |
XY-7 |
XY-8 |
2 |
Door Model |
Full Open Door |
Full Open Door |
3 |
Suitable Raw Materials |
Rubber/Plastic Products |
Rubber/Plastic Products |
4 |
Structure |
Horizontal Type Revolves |
Horizontal Type Revolves |
5 |
Reactor Size |
Φ2200*6000mm Φ2600*6600mm |
Φ2200*6000mm Φ2600*6600mm |
6 |
Capacity for One Batch |
5-6Mt; 8-10Mt |
5-6Mt; 8-10Mt |
7 |
Oil Yield of Tires |
40%-45% |
40%-45% |
8 |
Work Pressure |
Normal Pressure |
Normal Pressure |
9 |
Reactor Rotation Speed |
0.4R/M |
0.4R/M |
10 |
Fuels Choice |
Coal, Wood |
Coal, Wood, Gas, Oil |
11 |
Power |
18KW/H |
18-25KW/H |
12 |
Cooling Method |
Water Cycling |
Water Cycling |
13 |
Type of Drive |
External Annular Gear |
External Annular Gear |
14 |
Heating Method |
Direct |
Direct |
15 |
Type of Installation |
With Foundation |
With Foundation/Integrated Base |
16 |
Noise dB(A) |
≦85 |
≦85 |
17 |
Operation Mode |
Intermittent Operation |
Intermittent Operation |
18 |
Total Weight(MT) |
25-40 |
25-40 |
19 |
Installation Space Required |
30m*10m |
30m*10m |
20 |
Manpower |
3~4/batch |
3~4/batch |
21 |
Shipment |
Ф2200×6000=1*40HC+1*40FR Ф2600×6600=2*40HC+1*40FR |
Ф2200×6000=1*40HC+1*40FR Ф2600×6600=2*40HC+1*40FR |
Integrated Design Batch Waste Tyre Pyrolysis Plant
Integrated Batch Waste Tyre Pyrolysis Plant,Integrated Movable Waste Tyre Pyrolysis Plant,Large Capacity Used Tires Pyrolysis Plant,Integrated Batch Used Tyre Pyrolysis Plant
Shangqiu Jinpeng Industrial Co., Ltd. , https://www.recyclings.nl