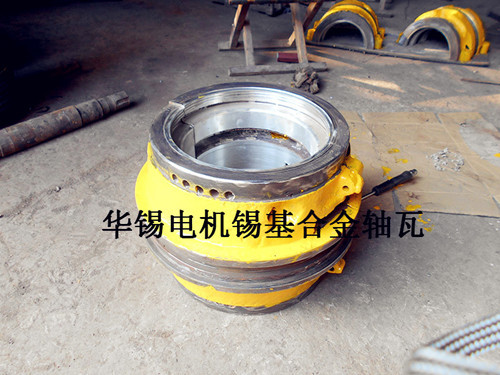
The main components of babbitt are tin, lead, bismuth and copper. Among them, niobium and copper are used to improve the strength and hardness of the alloy. Babbit alloys can be simply divided into three types: high-tin alloys, high-lead alloys, and master alloys (in which tin and lead all play an important role). In all of these alloys, niobium and copper are important alloying and hardening elements, and their structures are composed of hard, intermetallic compounds dispersed in a soft matrix.
The organization of babbitt metal alloys is characterized by uniform distribution of hard phase particles on the soft phase matrix. The soft phase matrix allows babbitt alloy to have very good hiding, compliance and seizure resistance, and after running-in, the soft matrix Concave, hard point convex, so that the formation of a small gap between the sliding surface, the oil storage space and lubricating oil channel, conducive to friction reduction; the upper convex hard point from the support role is conducive to bearing. In addition to the manufacture of plain bearings, babbitt alloys are often used as bearing bushes by spraying their wires or powder on steel or other substrates due to their soft texture and low strength. To prevent segregation of components and grain refinement, a small amount of arsenic is often added.
According to national standards, babbitt alloys can be divided into tin-based alloys and lead-based alloys. Lead-based alloys have lower strength and hardness than tin-based alloys and have poor corrosion resistance. Therefore, when customers use Babbit, they usually use tin-based alloys. The commonly used grades include ZChSnSb11-6, ZChSnSb8-4, and ZChSnSb8-8. Although the performance of lead-based alloys is not as good as that of tin-based alloys, many customers still choose to use them because they are more economical to use. Their commonly used grades include ZChPbSb16-16-2 and ZChPbSb1-16-1.
The casting method of babbitt alloy bushes summarized by professional manufacturer Zhoukou City Huaxi Alloy Technology Co., Ltd.:
Maintenance workshops often re-cast new linings of worn babbitt alloy bushings and continue to use them. The process includes: the preparation of the bottom tile, the smelting of the babbitt alloy, the clamping, casting and inspection of the bottom tile.
First, the preparation of the base tile
1. Melt the old Bab alloy liner
Clean the old bearing pads and heat the tile back evenly on the charcoal stove. When heated to 250-300°C, the tin-plated layer begins to soften, and the alloy layer is gently tapped with a tool, and then the remaining alloy is removed with a tool such as a spatula or a spatula.
2. Cleaning of the bottom tile surface
After removing the alloy layer, it is necessary to check whether the tin plating surface of the bottom tile is clean. If it is not clean, tin plating will be difficult, and the bonding quality between the alloy and the bottom tile is also difficult to guarantee. If dirt or oxide is present on the tin-plated surface of the base tile, it can be removed with sandpaper, wire brushes, etc. If there is sludge, put the bottom tile on a charcoal stove and heat it to 300-350°C. Then wipe with a tool such as a brush, a saturated zinc chloride solution or a 50% hydrochloric acid solution. Clean the floor tiles and never touch the oil.
3. Tin plated tin plate on the bottom
The bottom plating of the bottom shoe is used to make the babbitt metal and the bottom shoe more firmly and tightly. Because tin-bismuth cubic crystals and tin-copper cubic crystals in babbitt metal cannot be directly bonded with iron or copper, tin can bond well with iron and copper to form an intermediate alloy layer-metal compound. Tin plating should be as thin as possible. One of the reasons is that the metal compounds formed after tin plating are both hard and brittle. If they cannot penetrate into the bonding surface layers of babbitt and bottom tiles, their bonding quality will be affected. The second reason is that the thicker the tin plating layer, the easier it is to oxidize and affect the bonding quality. The process of tinning is to heat the cleaned bottom tile on the charcoal furnace to 260-300°C, then apply a layer of flux on the surface of the tin to be tinned, rub it with a tin strip, and then coat the tin with wood chips, etc. uniform. If uneven, rub with wood chips and other fluxes and then tin until uniform. The flux can be saturated solution of ammonium chloride or zinc chloride. The purity of the tin strip is preferably over 99.5%.
Second, the smelting of babbitt
When smelting, 65% to 70% of new babbitt metal and 30% to 35% of old babbitt metal can be used in combination, and attention should be paid to the cleaning of enamel, spoons, and iron bars used. In the repair workshop, the crucible can be made of A3 (Q235A) or stainless steel ladle, which facilitates direct casting. Melting crucibles can be heated on a charcoal stove to 400-500°C, then placed into a prepared Babella alloy block, and then sprinkled with a layer of 15-20mm thick charcoal. Adding the charcoal layer prevents oxidation of the Babbitt alloy, and the temperature can be determined by the color of the charcoal layer. When the temperature is 400 °C, charcoal shows a little red below, while the surface of babbitt is cherry red; when the temperature is 450 ~ 475 °C, the charcoal is burning. Of course, the smelting temperature can preferably be measured with a pyrometer. When the temperature of the alloy reaches the required level, use a spatula or other tool to dip into the crucible and stir to deoxidize, and then use a scoop to clear the slag to perform casting. The babbitt metal casting temperature is between 400 and 450 °C, and the heating temperature must not exceed 540 °C to prevent the alloy from burning.
Third, casting
The bottom tile should be cast immediately after being clamped. The utensils used for casting must be preheated and dried. Casting, pay attention to the slag, the flow should be uniform, not interrupted, to be cast once; the casting speed to master, too fast and easy to shrink holes, bubbles are prone to occur; alloy fluid can not follow the inner surface of the bottom tile Downstream, so as not to wash out the bottom tin. During the casting process, if the flow of the alloy melt in the mold is found to be degraded, the oxygen-acetylene flame can be used to uniformly heat the back of the bottom tile to improve the flow properties of the alloy melt and avoid the occurrence of cold separation. After casting, the back of the bearing pad is cooled with air to prevent segregation and reduce the difference in the shrinkage rates of the bottom tile and the babbitt alloy layer, reduce the residual stress, and avoid cracks and shelling. The alloy melt remaining after casting is cast into an ingot for future use.
IV. Inspection of casting quality
The surface of the cast babbitt should be uniform silver grey. If yellow is present, it indicates that the babbitt alloy is overheated. Use a small steel hammer to tap lightly along the surface of the alloy lining. If a crisp clinking sound is given, it means that the quality is acceptable; if a dull sound or sand noise is produced, it means that the alloy lining has cracks, voids, or the joint with the bottom tile is not tight. defect. If the above defects are found, scraping, repair welding or recasting may be carried out according to different conditions.
Huixian City Mishan Graphite Jip Co., Ltd. , https://www.msgraphitemold.com